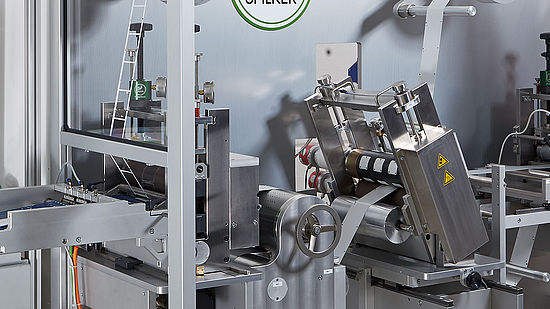
Convertingmaschinen für Medizinprodukte
Die Herstellung von Medikamenten unterliegt besonders strengen Vorschriften hinsichtlich Hygiene, Räumlichkeiten, Ausrüstung, Dokumentation und Kontrolle. Produziert wird unter Reinraum-Bedingungen, die Fertigungsanlagen müssen entsprechend hohen Anforderungen genügen. Das gilt auch für die jüngste Entwicklung der Spilker GmbH.
Für die Produktion von Schmerzpflastern konzipierte Spilker eine Rotationsmaschine, die unterschiedliche Spende-, Stanz- und Laminierprozesse mit dem abschließenden Prozess des rotativen Heißsiegelns kombiniert.
Die Bearbeitung anspruchsvoller Materialverbunde benötigt absolute Genauigkeit. Gerade bei Stanzprozessen sind eine äußerst präzise Stanzgeometrie und die exakte Stanztiefe entscheidend. Materialkombinationen aus Folien, Geweben oder Metallfolien im Verbund mit Klebern, Wirkstoffen und unterschiedlichsten Abdeckmaterialien erfordern eine Präzision bei der Verarbeitung, wie sie meist nur beim Rotationsstanzen erreichbar ist.
Sicherstellung der Produktqualität
Bei diesem Maschinenprojekt mussten verschiedenste Anforderungen an den Produktionsprozess, das Handling und die Sicherstellung der Produktqualität erfüllt werden. Und das begann bereits mit der Entwicklung der Rotationsmaschine. Auch bei diesem Projekt war die eigene Entwicklungs- und Konstruktionsabteilung im Haus ein wichtiger Baustein.
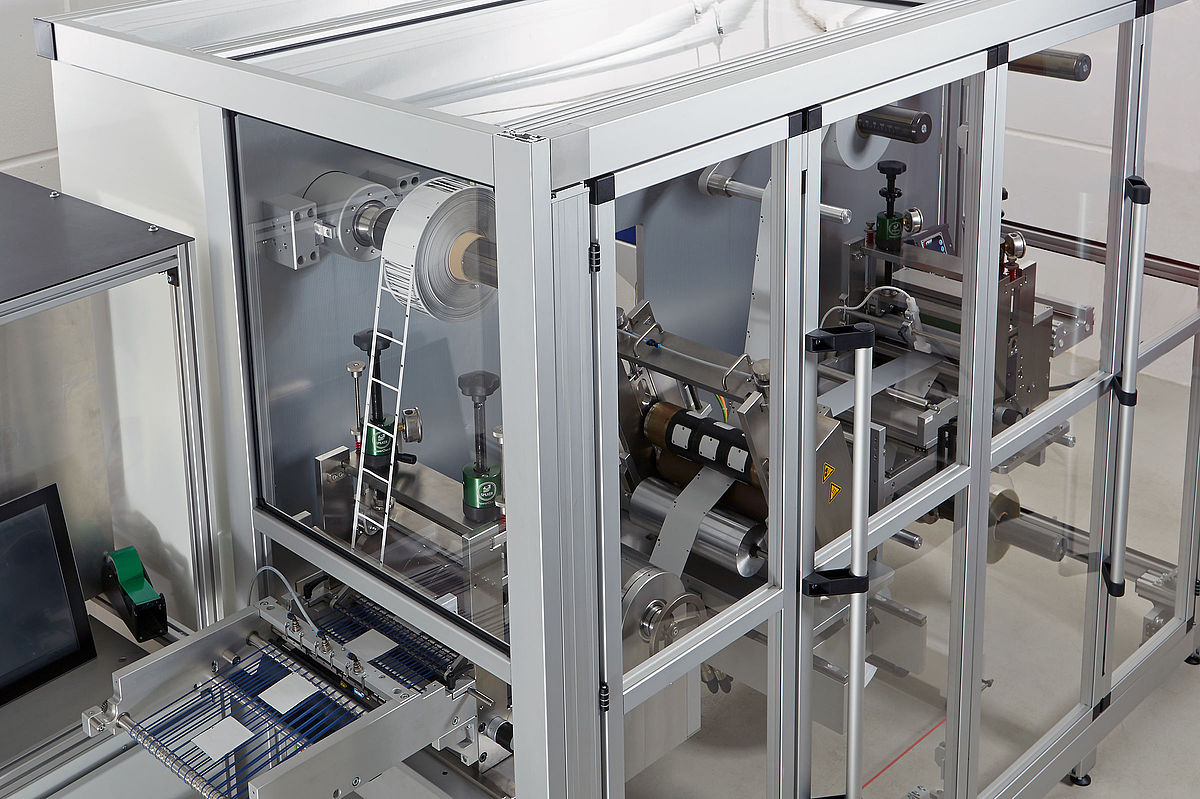
Die Ingenieure gestalteten mit Hilfe von 3D-CAD-Programmen erste Entwürfe und stimmten diese auf die individuellen Anforderungen ab. Dank den umfangreichen Simulationsfunktionen ermöglichte die Software eine reale Visualisierung des Projekts. Bei der Umsetzung des Entwurfs wird der Kunde fest eingebunden und kann jederzeit eigene Vorstellungen einbringen. Während der Entwicklungsphase werden, falls nötig, Prototypen und individuelle Werkzeuge hergestellt und getestet. Damit stellt Spilker sicher, dass die weiteren Anforderungen für einzelne Verarbeitungsschritte erfüllt werden.
In der Montage wurden die im eigenen Hause gefertigten Einzelteile zusammengefügt. Die Programmierung und Inbetriebnahme aller Komponenten erfolgte ebenfalls bei Spilker. Mit internen Testläufen und der Maschinenabnahme endete der eigentliche Entwicklungsprozess.
Dank der räumlichen Verbindung sämtlicher Produktionsschritte ergeben sich für das Unternehmen zahlreiche Vorteile. Die kurzen Wege zwischen den einzelnen Bereichen ermöglichen schnelle Kommunikation, die sich positiv auf die Produktionsgeschwindigkeit auswirkt.
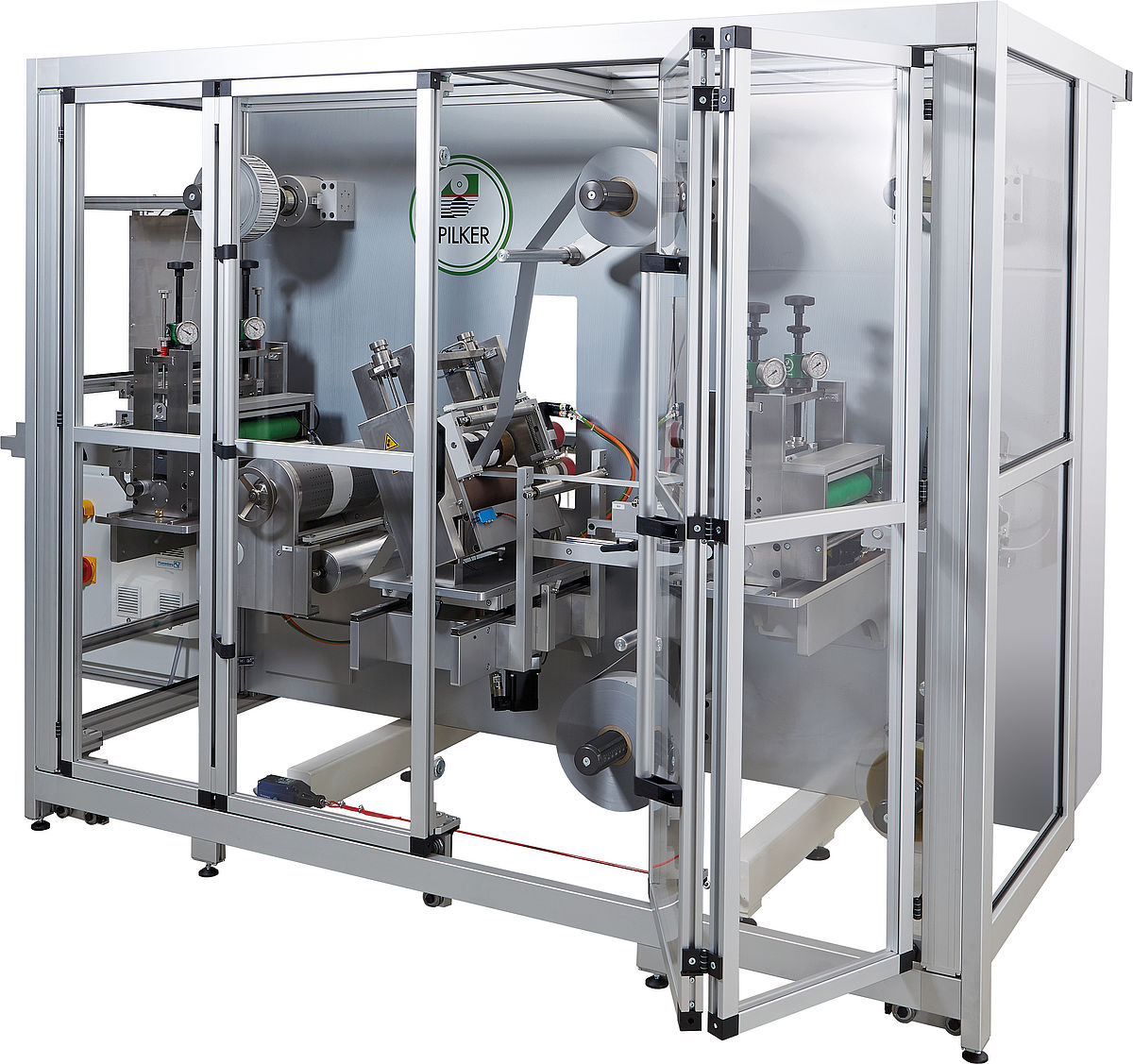
Die Abteilungen stehen stets in engem Kontakt, beispielsweise kann die Fertigung der Entwicklungsabteilung direktes Feedback geben, Änderungswünsche lassen sich einfach einbringen. Davon profitiert letztendlich auch der Kunde, der während der Konzept- und Produktionsphase eingebunden wird und maßgeschneiderte Lösungen erhält.
Bei dem Maschinenprojekt kommt für alle Antriebe Servotechnologie zum Einsatz. Die Bedienung erfolgt über ein 24 Zoll Multitouch Display mit einer Benutzeroberfläche, die von Spilker eigens dafür entwickelt wurde.
Modernste Technik im Einsatz
Die Produktionsgeschwindigkeit beträgt 30 Meter pro Minute bei einer maximalen Bahnbreite von 300 mm, was bei dem hohen Anforderungsprofil des Produktes ausgesprochen schnell ist und die Produktivität deutlich unterstreicht. Durch den modularen Aufbau ist es möglich, beispielsweise Inspektions- und Drucksysteme zusätzlich zu integrieren oder weitere Verarbeitungsschritte hinzuzufügen. Mit einer Länge von 3,5 Metern, einer Tiefe von einem Meter und einer Höhe von 1,8 Metern ist die Maschine überraschend kompakt und fügt sich problemlos auch in enge Produktionsumgebungen und vorhandene Abläufe ein.
Die maschinell gefertigten Rotationswerkzeuge entsprechen den hohen Anforderungen der Pharmaindustrie und können mit verschiedenen lebensmittelkonformen Beschichtungen versehen werden. Für alle Werkzeug- und Maschinenteile werden Materialien eingesetzt, die einen maximalen Korrosionsschutz sicherstellen.
Um zusätzlich Hygiene und Sicherheit zu gewährleisten, ist die Maschine von einer Schutzeinhausung aus Acrylglas und eloxierten Aluminiumprofilen umgeben. Die Einhausung lässt sich auf der gesamten Maschinenlänge öffnen, damit alle Bereiche der Maschine problemlos zugänglich sind. Durch das Acrylglas bleibt der Innenraum hell, und es ist eine optimale Sicht auf die Maschine möglich.
Das von einer Rolle einlaufende Pflastermaterial wird zunächst vereinzelt, und es wird ein Einschnitt zum leichten Öffnen der einzelnen Pflaster gestanzt. Durch statische Aufladung werden die Pflaster danach auf dem unteren Siegelmaterial exakt auf Position gehalten. Die Materialbahn mit den Pflastern wird mit einer zweiten Bahn Siegelmaterial durch Hitze luftdicht verschlossen. Die fertig versiegelten Pflaster werden bei einem weiteren Stanzprozess vereinzelt und auf einem Auslageband ausgegeben.
Wenn auch Sie Unterstützung bei einem Projekt benötigen, finden sie hier den richtigen Ansprechpartner.
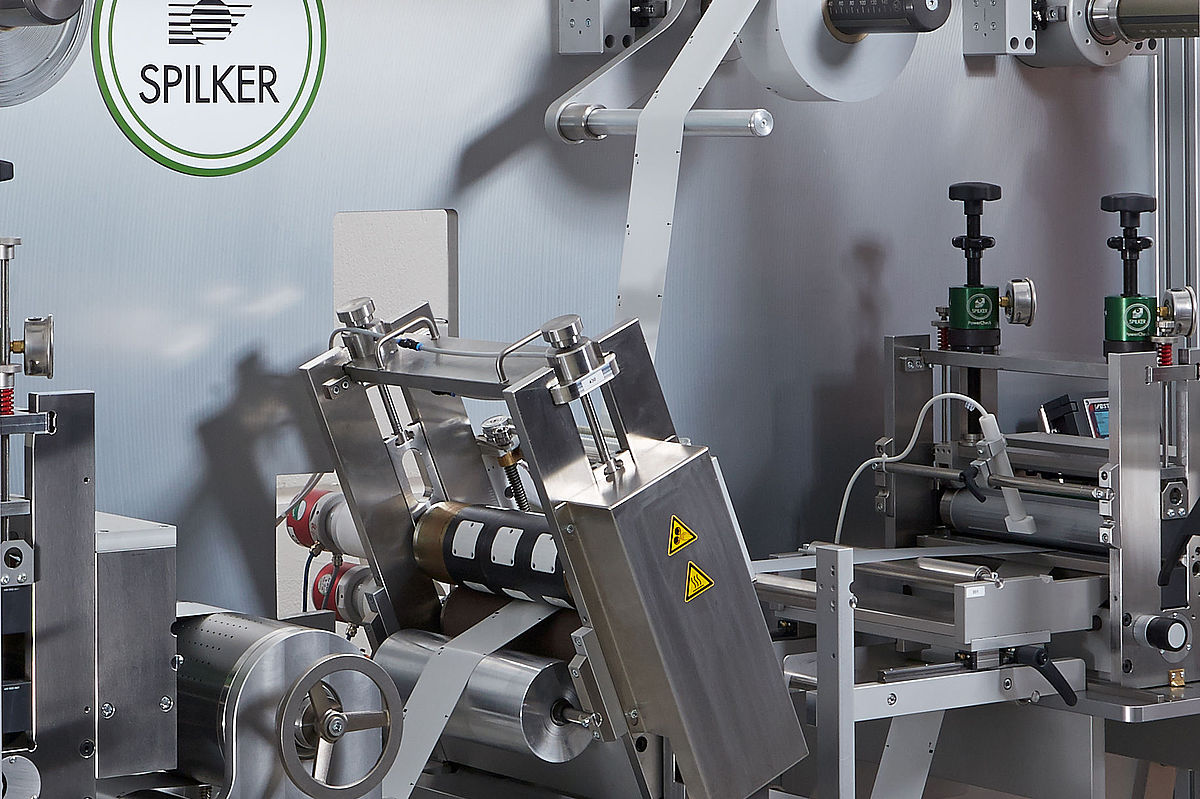